1. Introduction to ISO 13485
ISO 13485 is a global standard for quality management systems in the medical device industry. It outlines specific requirements for QMS. This standard ensures that medical device companies consistently meet customer and regulatory requirements by emphasizing risk management, quality controls, and continuous improvement. Implementing ISO 13485 helps companies improve their operational efficiency, reduce risks, and enhance product quality, thereby ensuring patient safety and satisfaction.
2. How to Get ISO 13485 Certification and Installation of a QMS
Steps to obtain ISO 13485 Certification:
- Perform a gap assessment: Evaluate your current processes against ISO 13485 requirements to identify areas needing improvement.
- Documentation: Develop comprehensive documentation for QMS, including quality manuals, procedures, and records.
- Implement the QMS by introducing it and ensuring integration of all procedures and processes into daily operations.
- Internal Audit: Conduct internal audits to verify compliance and effectiveness of the QMS.
- Management Review: Management reviews the QMS performance and addresses any areas needing improvement.
- Certification Audit: Engage a certification body to perform an external audit. This audit consists of two stages: a documentation review and an on-site audit.
Installing a QMS Involves:
- Planning: Define the scope, objectives, and resources needed for QMS implementation.
- Development: Develop processes for quality control, risk management, and regulatory compliance.
- Integration: Ensure the QMS integrates seamlessly with existing systems like ELN (Electronic Laboratory Notebooks) and LIMS (Laboratory Information Management Systems).
- Training: Provide comprehensive training for staff on QMS procedures and requirements.
- Monitoring and Improvement: Regularly monitor and measure QMS performance and make necessary improvements.
3. Overview of ISO 13485 Requirements
Key Requirements of ISO 13485:
- Senior management must commit to the QMS, ensuring clear definition of roles, responsibilities, and authorities. This includes establishing a quality policy and setting quality objectives aligned with customer requirements and regulatory standards.
- Resource Management: Ensure adequate resources, including qualified personnel, appropriate infrastructure, and suitable work environments, are available to implement and maintain the QMS.
- Product Realization: Plan and develop processes necessary for product realization, from design and development to delivery. This includes defining customer requirements, design control, purchasing controls, production, and service provision.
- Measurement, Analyze, and Improvement: Implement procedures for monitoring, measurement, analysis, and improvement of processes and products. This involves conducting internal audits, managing non-conformities, and taking corrective and preventive actions to ensure continuous improvement.
4. Why Use a Contract Manufacturer
Advantages of Using a Contract Manufacturer:
- Expertise: Access specialized knowledge and skills in medical device manufacturing, ensuring high-quality products and compliance with regulatory standards.
- Cost Efficiency: Reduce capital expenditure on equipment and operational costs associated with maintaining manufacturing facilities.
- Scalability: Easily scale production up or down based on demand without the need for significant investment in infrastructure.
- Compliance: Leverage the contract manufacturer’s experience in complying with ISO 13485 and other relevant standards, ensuring your products meet regulatory requirements.
5. How Much Does it Cost to Get ISO 13485
Factors Influencing the Cost of ISO 13485 Certification:
- Company Size: Larger companies may face higher costs because of the complexity and scale of their operations.
- Scope of Certification: The breadth of processes and products covered by the QMS can impact costs. A wider scope typically requires more resources for implementation and auditing.
- Consultancy Fees: Hiring consultants for gap analyzing, documentation, and implementation support can add to the expense.
- Training Costs: Expenses for training employees on QMS procedures and requirements.
- Certification Body Fees: Fees charged for the audit process, including reviewing documents and conducting on-site audits.
Estimated Costs:
- Small Companies: $10,000 - $20,000
- Medium Companies: $20,000 - $50,000
- Large Companies: $50,000 - $100,000+
6. What Controls Do ELN/LIMS/QMS Need to Satisfy for Your Lab
For compliance with ISO 13485, ELN, LIMS, and QMS systems need to ensure the following quality management requirements:
- Data Integrity: Secure and accurate data recording, storage, and retrieval. This involves implementing robust data entry protocols, validation checks, and ensuring traceability of data.
- Traceability means tracking quality data and processes to trace each step in manufacturing back to its source.
- Manage documents efficiently to ensure using the latest versions for Document Control. This includes document approval, distribution, and change control processes.
- Risk Management: Identification and mitigation of risks throughout the product lifecycle. This involves conducting risk assessments, implementing control measures, and regularly reviewing risk management processes.
- Audit Trails: Detailed audit trails to demonstrate compliance during inspections. These trails should capture all changes and actions taken within the QMS, providing a clear history of events.
The above listed QMS requirements ensure that we meet the reporting requirements for ISO 13485. Companies often need to prepare the following reports to meet the audit requirements:
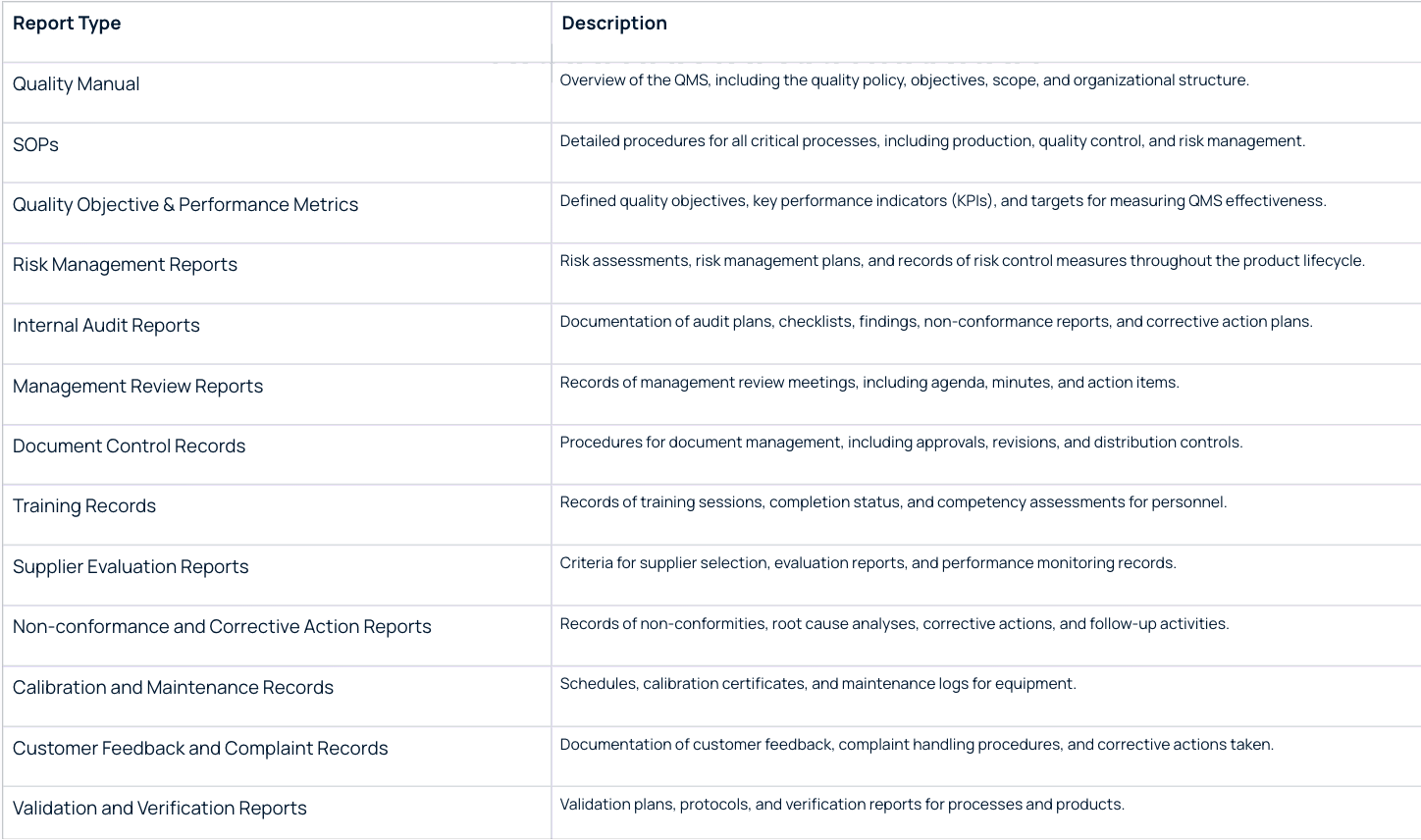
7. How Scispot Satisfies ISO 13485 Controls
Scispot, as a Modern ELN, LIMS, and QMS, Satisfies the Following ISO 13485 Controls:
- Data Integrity: Scispot ensures secure and accurate data recording, storage, and retrieval. It incorporates robust data entry protocols, validation checks, and ensures data traceability.
- Traceability: Scispot tracks quality data and processes, making it easy to trace each step back to its origin.
- Scispot ensures efficient document management by providing access to the latest versions for relevant personnel.
- Risk Management: Scispot includes tools for identifying and mitigating risks throughout the product lifecycle. It supports regular risk assessments and updates.
- Audit Trails: Scispot maintains detailed audit trails to demonstrate compliance during inspections. It captures all changes and actions within the QMS, providing a clear history of events.
- Scispot easily connects with many other tools for document control. It also includes document versioning and management features.
Process to achieve certification
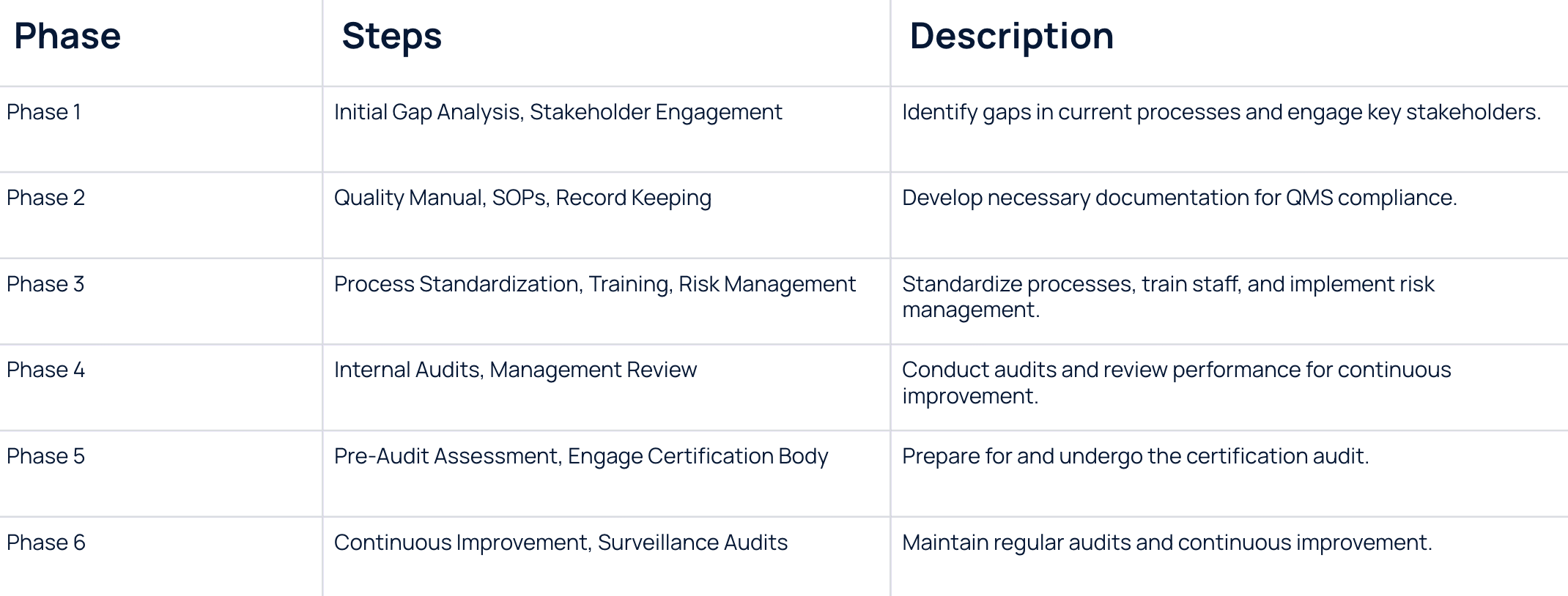
8. Enhancing Your ISO 13485 Certification Process
Risk Management in ISO 13485:
Effective risk management is crucial in ISO 13485 compliance. It involves identifying potential risks in design and manufacturing, assessing their impact, and implementing measures to mitigate them. Regular risk assessments and updates ensure new risks are promptly addressed.
Supplier Management:
Maintaining high-quality standards extends to supplier management. ISO 13485 requires robust procedures for selecting and monitoring suppliers, including performance evaluations and adherence to regulatory requirements.
Post-Market Surveillance:
Post-market surveillance involves ongoing monitoring of medical device performance after market release, collecting and analyzing data to identify potential issues and implementing corrective actions.
Change Control:
A well-defined change control process ensures that modifications in processes, products, and documentation are evaluated for impact on quality and regulatory compliance before implementation.
Customer Feedback:
Systematically collecting and analyzing customer feedback helps identify areas for improvement and enhance customer satisfaction.
Training and Competence:
Ensuring that all personnel involved in the QMS are adequately trained and competent is crucial. This involves regular training programs, competency assessments, and maintaining training records.
Medical device companies can improve their quality management systems by focusing on these areas and staying compliant with ISO 13485.
Summary
ISO 13485 provides a comprehensive framework for quality management in the medical device industry, ensuring compliance with regulatory standards and consistent product quality. Certification involves meticulous preparation, implementation, and regular monitoring. Contract manufacturers offer expertise and cost savings. ELN, LIMS, and QMS systems must guarantee data integrity and traceability to meet regulatory requirements.